Interview 007
株式会社 川口金属加工
2014年入社/
兵庫工場 製造部 圧延課主任
岡本 昌
圧延の未来形へ。熟練の技と
最新技術の融合を図る。
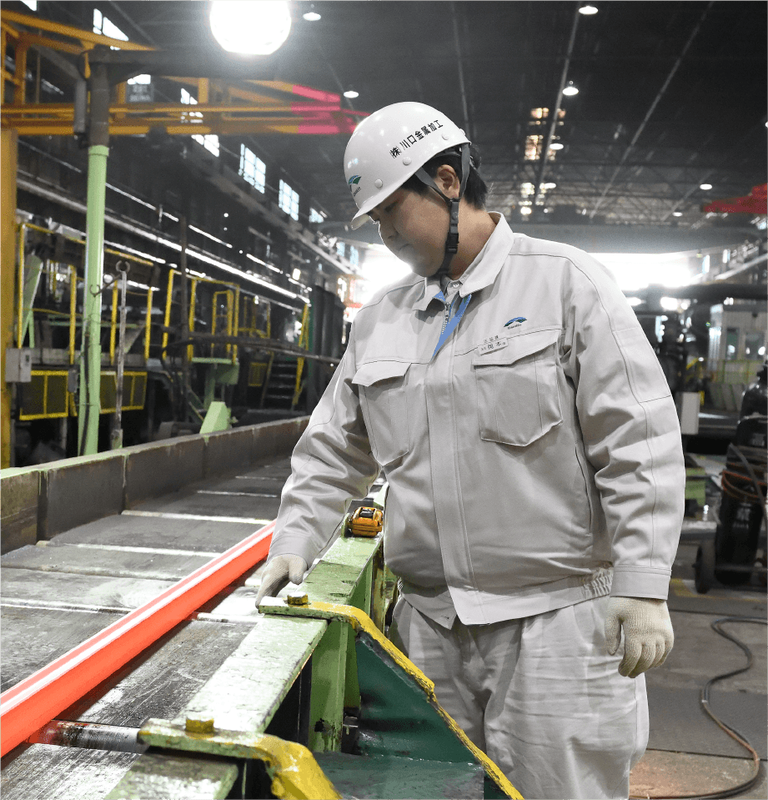
過去から未来へ、鉄の潜在能力を引き出す!
私が就職を考え始めた大学 4 年の頃は、折り悪くリーマンショックの 後でした。そこで大学院に進学し、さらに半導体の材料工学を専攻して様々な金属材料について学びました。
就職活動ではモノづくりで広い業種を対象に考え様々な会社に見学に伺いましたが、弊社に就職した研究室の先輩が話していた、「積極的に若手の成長・活躍の場を作る姿勢」や、川口金属工業をはじめ、個性あるモノづくり企業が連携した川金ホールディングスへ惹かれました。また、弊社は熱間圧延という金属加工技術のパイオニアで、高温に熱した鉄の角材をローラーに通して圧力をかけ、様々な形状に加工した製品を製造しています。
曽祖父が高知県の刃物が有名な町で刀鍛冶をしていました。鍛造と呼ばれ、刀鍛冶が真赤に焼いた鉄を叩きながら刃物を作り出す伝統技術を近くで見て育った私としては昔から鉄には親しみを感じており弊社の圧延技術に興味を抱きました。これらの繋がりもあって弊社に決めました。
ある一日のスケジュール
- 8:30
- 車で出勤後、メールチェック。続いて生産量や不良率など、前日の製造状況をデータで確認。
- 12:45
- 午後からは工場の各現場を回り、稼働状況を確認。製造担当の意見や要望をヒアリング。
- 13:30
- 導入予定の設備機械の件で、候補A社の担当が来社。ラインを回りながら状況を説明。
- 16:00
- 事務所に戻って日課の事務処理へ。工場から上がるデータをチェックし、明日に備える。
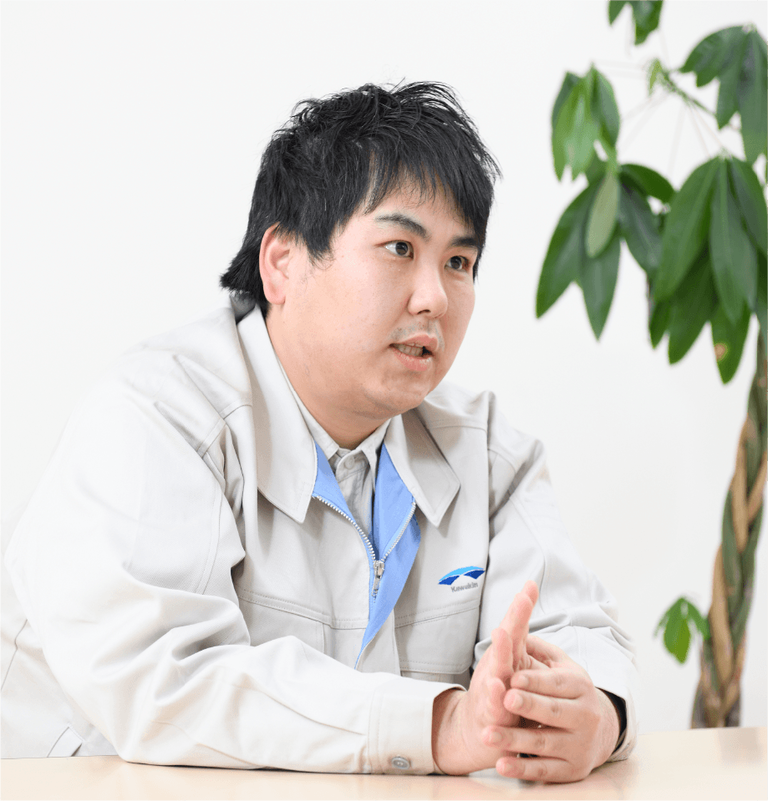
若手が自ら考え、行動して成長できる場
入社後3ヶ月は作業抜きで各現場を周り、全工程を確認しながら理解 を深めます。その後1年目までは与えられたテーマに基づく改善プロ ジェクトに加わります。私が取り組んだのは加熱炉と呼ばれる鋼材燃焼設備における燃焼制御の改善でした。燃焼が制御できないと必要以上に設備内の酸素と鋼材中の炭素が結合し抜けて、完成品が脆くなってしまう「脱炭」による品質低下の問題が発生します。
弊社の製品は製造機器や免震装置のスライド可動部、車のドアのヒンジなどに使われており高品質が求められるので、精度や強度が落ちる「脱炭」は極力抑えたい現象です。ところがこの解決が容易ではなく、加熱炉の燃焼制御が失敗すると品質問題や不完全燃焼による環境への悪影響も及ぼしかねない難しい問題でした。
そこで私は、解決法を探るため燃焼制御を一から勉強しながら過去の 製造記録を遡り、この現象が起こりやすい状況を丹念に調べて原因を追求することで、ついには脱炭の発生率の抑制に成功し環境面でも燃焼制御による改善ができました。もちろん上司や熟練の職工さんの指導や協力があっての成果ですが、入社早々にプロジェクトのリーダーを任され、品質向上に貢献できた経験は、大きなやりがいと自信に繋がりました。
熟練の技と革新技術の融合を目指して
6年目の現在は圧延課の主任として、操業管理や工場内の改善業務を担当しています。不良を作らず、かつ生産効率を上げる方法を常に模索しており、最近では3Dスキャナを導入しました。従来は投影機で拡大したシルエットを手書きで記録し、お客さまの要望通りの形状に仕上がっているかを確認していましたが、3Dスキャナにより効率も精度も一挙に向上しました。さらには不良の選別にも役立っています。
その一方で、微妙な温度変化やミクロン単位の傷などを直感的に察知し、的確に判断する熟練の職工さんの勘の鋭さには感嘆します。我々若手には写真で拡大しても一目では傷がわかりませんが、見分け方をアドバイスされると、不思議と見えるようになるのです。そんな熟練工の見極めのポイントを最新のカメラやセンサー技術でデータ化して蓄積し、また現場の状況も最新の技術でリアルタイムに把握しながらIoTで制御する。そんな未来形を構想しています。
工場長や今は定年退職された前圧延課課長から「教科書で学ぶ内容は論理的に仕事を進める上で重要だが、実際にモノを作っている現場も同様に大切である」と教えてもらいました。現実には数値では語れない現象も出ますし、それがモノという結果にも出ます。過去の記録をビッグデータ化し、IoTでハイテク化を進めても、経験を積んだ人間には敵わない部分もあります。双方の優れた点をうまく融合して、お客さまに満足いただける「最良の製品」を創り出して行きたいですね